26.11.2018
2 minutes of reading
At the Annual General Meeting of the European CHEERS project held at IFP Energies nouvelles (IFPEN) on November, the nine partners endorsed the launch of a large-scale model (equivalent to 1.5 MW) developed for the demonstration of Chemical Looping Combustion (CLC), an innovative CO2 capture technology.
The chemical looping combustion process was developed by IFPEN and Total at a laboratory scale and on a 10 KW pilot unit located at IFPEN’s Lyon site.
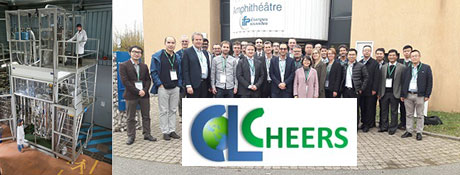
The model stage of the CHEERS project is aimed at validating the technology before building a demonstration unit to validate the performance of the process on a pre-industrial scale. Constructed in a technical center run by Chinese energy company Dongfang Boiler Co, the unit with a capacity of at least 3 MWth, operated with petcoke (a refining industry residue that will be recovered to produce steam and electricity), will be the most powerful anywhere in the world.
If the R&D project proves successful, the first fully operational industrial facility could be a reality by 2025.
This experiment is being conducted within the context of the CHEERS (Chinese European Emission Reducing Solutions) project, jointly funded by the European Union (Horizon 2020 program) and the Chinese Ministry of Sciences and Technologies.
The aim of the project is to demonstrate a disruptive technology designed to capture industrial CO2 emissions more efficiently and at a more competitive cost.
Lasting five years (2018/2022), CHEERS brings together players with a long track record in Carbon-Capture Use and Storage (CCUS):
- IFPEN,
- Total,
- SINTEF (project coordinator),
- Tsinghua University,
- Dongfang Boiler Co.
According to the International Energy Agency, CCUS could be making a significant contribution to the efforts required to limit global warming to 2°C by 2100.
How does CLC work?
Oxycombustion capture consists in burning hydrocarbons in the presence of pure oxygen instead of air, making it possible to obtain flue gases with a higher CO2concentration (concentration of above 90%) and to facilitate its capture.
The main obstacle to the use of this technology is related to the separation of oxygen from air, something that is generally done via cryogenic distillation, which is not only expensive but also very energy-intensive.
To avoid the cost of this separation, the Chemical Looping Combustion (CLC) process uses a metal oxide to transport oxygen to the combustion zone without combining it with nitrogen from air.
There are two advantages associated with CLC:
- a low energy penalty because the oxygen is separated from air by means of a metal oxide,
- and the option to treat a bigger variety of feedstock: natural gas, heavy fuel, coal, biomass or even petcoke as envisaged for the CHEERS project.
CO2 capture, utilization and storage