Like all sectors concerned by electrification, the transport sector requires the design of high-performance, efficient electrical systems that respond to multiple constraints, such as cost and compactness. In this context, optimisation has become an essential step in the design process of these systems, particularly for electrical machines.
When designing an electrical machine, methods based on finite elements, recognised for their accuracy and generic nature, are often used to simulate its performance. However, due to their relatively long computation times, the use of these methods in optimisation loops is penalizing, all the more so in the case of stochastic optimisation algorithms which themselves require a large number of computations.
Research work is being carried out within the “Mobility and Systems” Division1 to propose new optimisation methodologies intended to address this computation time issue. Approaches such as the use of substitution models are already in use [1]. Other approaches, such as Bayesian optimisation2 and multifidelity optimisation, are also being considered. In addition to reducing computation time, these approaches could lead to more relevant modelling and optimization of the power system under study, by enabling more complete consideration of the physical phenomena governing its behavior.
Once the electrical machine designed, ensuring its correct behavior under all operating conditions involves developing and implementing control laws and diagnostic solutions that will serve to control it in the best possible way.
The global approach developed and used for the control and diagnosis of electrical machines is illustrated in Figure 1.
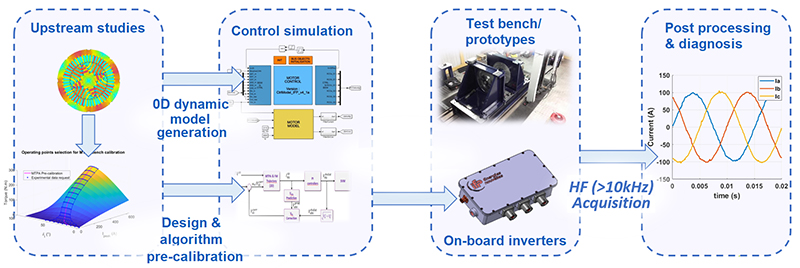
In terms of control, dedicated algorithms have been developed within the department to ensure optimum and robust behavior over the entire operating range. These algorithms use design data and an automatic code generation system to speed up the software implementation phase in the inverter control boards also developed by IFPEN.
On the subject of diagnosis, research work is being carried out to develop fault indicators for monitoring the health of stators and rotors:
- In the case of stator monitoring, the idea is to monitor the ageing of the insulation so as to anticipate the appearance of serious inter-turn short-circuit faults. A wavelet transform method has therefore been developed to identify and locate incipient inter-turn defects [2] ;
- In the case of rotor monitoring, the aim is to supervise the magnets, to detect the appearance of demagnetization faults and thus anticipate any drop in the machine performance. A finite element approach has enabled us to develop an indicator of this type of fault by using the zero sequence component of the back electromotive forces [3].
On these two types of defect, a gain in terms of detection sensitivity is expected through a behavioral approach in the high-frequency zone, currently under development. Our work focuses on modelling phenomena and developing dedicated signal processing methods. In addition, to obtain a good compromise between calculation time and accuracy of results, hybrid simulations, combining finite element calculations and based on equivalent electrical circuit models, have been adopted3.
The modelling, optimization, the control and the diagnosis of electrical machines, carried out by the “Mobility and Systems” division, cover the entire life cycle of electrical machines, from the design phase, through commissioning and performance validation, to monitoring their operation under real-life conditions.
1- By the "Electrical and Electronic Systems" division, in collaboration with the "Applied Mathematics" department of the "Digital Science and Technology" division.
2- Thesis by Adan Reyes Reyes : “Contribution méthodologique au dimensionnement optimal et robuste des machines électriques dédiées aux chaines de traction VE et VEH”.
3- Thesis by Jérémy Creux: “Modélisation hautes fréquences des machines synchrones à aimants, Application à la détection précoce des défauts inter-spires et des défauts de désaimantation”.
Bibliographic references
-
A. R. Reyes, A. Nasr, D. Sinoquet and S. Hlioui, Robust design optimization taking into account manufacturing uncertainties of a permanent magnet assisted synchronous reluctance motor, 2022 IEEE International Conference on Electrical Sciences and Technologies in Maghreb (CISTEM), Tunis, Tunisia, 2022, pp. 1-6.
>> https://doi.org/10.1109/CISTEM55808.2022.10043885
-
N. Haje Obeid, A. Battiston, T. Boileau and B. Nahid-Mobarakeh, Early Intermittent Interturn Fault Detection and Localization for a Permanent Magnet Synchronous Motor of Electrical Vehicles Using Wavelet Transform, in IEEE Transactions on Transportation Electrification, vol. 3, no. 3, pp. 694-702, Sept. 2017.
>> https://doi.org/10.1109/TTE.2017.2743419
-
J. Creux, N. H. Obeid, T. Boileau and F. Meibody-Tabar, Local Demagnetization Fault Detection in PMASynRM based on Finite Element Modeling and Characterisation, IECON 2022 – 48th Annual Conference of the IEEE Industrial Electronics Society, Brussels, Belgium, 2022, pp. 1-6.
>> https://doi.org/10.1109/IECON49645.2022.9968829
Scientific contacts: andre.nasr@ifpen.fr - najla.haje-obeid@ifpen.fr