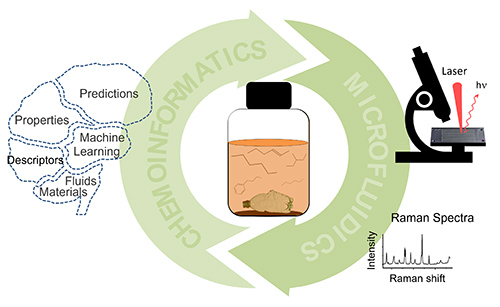
For many industrial applications, such as the chemical recycling of plastics, or in order to ensure compatibility between polymers and new fuels, it is essential to anticipate interactions between materials and fluids. Bringing them into contact with each other can trigger ageing phenomena resulting in a loss of their initial performances. It is thus crucial to have a better understanding of these phenomena and the subsequent degradation kinetics in order to be able to design equipment as precisely as possible.
The ageing of materials in the presence of a fluid can be evaluated by measuring the mass of samples of a few cubic centimeters immersed in the fluids concerned over variable periods of time. The major drawbacks with this method are that it requires extremely long and expensive experimental campaigns and it is poorly adapted to some specific situations: sensitive products or conditions (toxicity, potential dangers, extreme temperature and pressure conditions, etc.). To overcome this problem, two possible options are being rolled out together at IFPEN: the development of predictive models and the reduction of experimental scale.
The first option involves turning to Chemoinformatics, one aspect of which is the use of artificial intelligence to predict properties on the basis of reference data [1]. Its application has already made it possible to model the quantity of fluid penetrating a polymer during prolonged contact between the two [2]. In order to increase the number of potential applications of these models (new polymer/fluid pairings, other temperature and pressure ranges, etc.) or make them more robust, it is now important to supplement existing data via the large-scale and targeted acquisition of new experimental results. To achieve this, new techniques need to be considered.
To this end, the field of Microfluidics broadens the spectrum of experimental options. This technique consists in studying the behavior of fluids and/or materials in miniaturized systems, such as chips, containing channels a few tens of micrometers in diameter (Figure 1). This scale reduction offers considerable advantages in terms of cost, experimental safety and time. The small volumes involved reduce the quantities of matter required and limit operating risks. Moreover, the method is naturally suitable for “high-throughput” experimental data production (parallelization, acceleration via surface/volume ratio increase). In addition, combining non-destructive methods, such as Raman spectroscopy, makes it possible to study phenomena in situ, including in harsh conditions, due to the fact that these chips are able to function in high-pressure, high-temperature conditions [3].
All these aspects make the combined use of Chemoinformatics and Microfluidics for studying material-fluid interactions an obvious solution. More broadly, their combination opens up interesting new avenues for the development of robust models, i.e., based on numerous and relevant data, and capable of also taking into account new compounds as well as new pressure and temperature conditions.
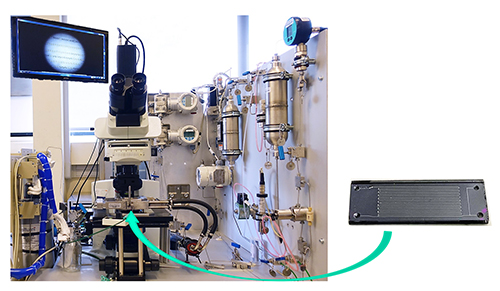
References:
- Science@ifpen issue 48, June 2022
>> https://www.ifpenergiesnouvelles.com/brief/cheminformatics-and-its-descriptors-application-polymerfluid-compatibility
- B. Creton, B. Veyrat, M.-H. Klopffer, Fuel sorption into polymers: experimental and machine learning studies, Fluid Phase Equilibria 2022, 556, 113403.
>> DOI: 10.1016/j.fluid.2022.113403
- T. Gavoille, N. Pannacci, G. Bergeot, C. Marliere, S. Marre, Microfluidic approaches for accessing thermophysical properties of fluid systems, Reaction Chemistry & Engineering 2019, 4(10), 1721-1739.
>> DOI: 10.1039/C9RE00130A
Scientific contacts: benoit.creton@ifpen.fr ; claire.marliere@ifpen.fr